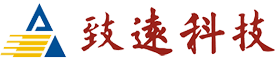
-
- English
一、铝合金再生生产典型工艺
1.1.1再生铝熔炼工艺特点
再生铝是以回收来的废铝零件或生产铝制品过程中的边角料以及废铝线等为主要原材料,经熔炼配制生产出来的符合各类标准要求的铝锭。这种铝锭采用回收废铝,而有较低的生产成本,而且它是自然资源的再利用,具有很强的生命力,特别是在当前科技迅猛发展,人民生活质量不断改善的今天,产品更新换代频率加快,废旧产品的回收及综合利用已成为人类持续发展的重要课题,再生铝生产也就是在这样的形式下应运而生并具有极好的前景。
由于再生铝的原材料主要是废杂铝料,废杂铝中有废铝铸件(以Al-Si合金为主)、废铝锻件(Al-Mg-Mn、Al-Cu-Mn等合金)、型材(Al-Mn、Al-Mg等合金)废电缆线(以纯铝为主)等各种各样料,有时甚至混杂入一些非铝合金的废零件(如Zn、Pb合金等),这就给再生铝的配制带来了极大的不便。如何把这种多种成分复杂的原材料配制成成分合格的再生铝锭是再生铝生产的核心问题,因此,再生铝生产流程的第一环节就是废杂铝的分选归类工序。分选得越细,归类得越准确,再生铝的化学成分控制就越容易实现。
废铝零件往往有不少镶嵌件,这些镶嵌件都是些以钢或铜合金为主的非铝件,在熔炼过程中不及时地扒出,就会导致再生铝成分中增加一些不需要的成分(如Fe、Cu等)因此,在再生铝熔炼初期,即废杂铝刚刚熔化时就必须有一道扒镶嵌件的工序(俗称扒铁工序)。把废杂铝零件中的镶嵌件扒出,扒得越及时、越干净,再生铝的化学成分就越容易控制。扒铁时熔液温度不宜过高,温度的升高会使镶嵌件中的Fe、Cu元素溶入铝液。
各地收集来的废杂铝料由于各种原因其表面不免有污垢,有些还严重锈蚀,这些污垢和锈蚀表面在熔化时会进入熔池中形成渣相及氧化夹杂,严重损坏再生铝的冶金质量。清除这些渣相及氧化夹杂也是再生铝熔炼工艺中重要的工序之一。采用多级净化,即先进行一次粗净化,调整成分后进行二级稀土精变,再吹惰性气体进一步强化精炼效果,可有效的去除铝熔液中的夹杂。
废铝料表面的油污及吸附的水分,使铝熔液中含有大量气体,不有效的去除这些气体就使冶金质量大大下降,强化再生铝生产中的除气环节以降低再生铝的含气量是获得高质量再生铝的重要措施。
二、再生铝的熔炼
2.1熔炼的目的
金属合金熔炼的基本任务就是把某种配比的金属炉料投入熔炉中,经过加热和熔化得到熔体,再对熔化后的熔体进行成分调整,得到合乎要求的合金液体。并在熔炼过程中采取相应的措施控制气体及氧化夹杂物的含量,使符合规定成分(包括主要组元或杂质元素含量),保证铸件得到适当组织(晶粒细化)高质量合金液。
由于铝元素的特性,铝合金有强烈的产生气孔的倾向,同时也极易产生氧化夹杂。因此,防止和去除气体和氧化夹杂就成为铝合金熔炼过程中最突出的问题。为了获得高质量的铝合金液,对其熔炼的工艺就必须严格把关,并采取措施从各个方面加以控制。
2.2 熔炼工艺
铝合金熔炼过程如下:
装炉→熔化(加铜、锌、硅等)→扒渣→加镁、铍等→搅拌→取样→调整成分→搅拌→精炼→扒渣→转炉→精炼变质及静置→铸造。
装炉 正确的装炉方法对减少金属的烧损及缩短熔炼时间很重要。对于反射炉,炉底铺一层铝锭,放入易烧损料,再压上铝锭。熔点较低的回炉料装上层,使它最早熔化,流下将下面的易烧损料覆盖,从而减少烧损。各种炉料应均匀平坦分布。
熔化 熔化过程及熔炼速度对铝锭质量有重要影响。当炉料加热至软化下榻时应适当覆盖熔剂,熔化过程中应注意防止过热,炉料熔化液面呈水平之后,应适当搅动熔体使温度一致,同时也利于加速熔化。熔炼时间过长不仅降低炉子生产效率,而且使熔体含气量增加,因此当熔炼时间超长时应对熔体进行二次精炼。
扒渣 当炉料全部熔化到熔炼温度时即可扒渣。扒渣前应先撒入粉状熔剂(对高镁合金应撒入无钠熔剂)。扒渣应尽量彻底,因为有浮渣存在时易污染金属并增加熔体的含气量。
加镁与加铍 扒渣后,即可向熔体中加入镁锭,同时应加熔剂进行覆盖。对于高镁合金,为防止镁烧损,应加入0.002%~0.02%的铍。铍可利用金属还原法从铍氟酸钠中获得,铍氟酸钠是与熔剂混合加入。
搅拌 在取样之前和调整成分之后应有足够的时间进行搅拌。搅拌要平稳,不破坏熔体表面氧化膜。
取样 熔体经充分搅拌后,应立即取样,进行炉前分析。
调整成分 当成分不符合标准要求时,应进行补料或冲淡。
熔体的转炉 成分调整后,当熔体温度符合要求时,扒出表面浮渣,即可转炉。
熔体的精炼 变质成分不同,净化变质方法也各有不同。
2.3 成分调整
在熔炼过程中,金属中各元素均由于它们自身的氧化而减少,它们被氧化程度的多少,不仅与本身对氧的亲和力的大小有关之外,还与该元素在液体合金中的浓度(活度)、生成氧化物的性质、以及所处的温度等因素有关。一般来说,对氧亲和力较大的元素损失多些,铝、镁、硼、钛和锆等对氧亲和力很强;碳、硅、锰等其次;铁、钴、镍、铜及铅等较弱。所以,在熔炼合金中对氧亲和力较强的元素,将要被“优先氧化”而造成过多的损耗;相反,那些对氧亲和力较弱的元素,则能相对的受到“保护”而损耗少些。
通过熔炼后,合金化学成分中某元素因氧化损耗而使其含量增加或降低,应视该元素与基体金属元素的相对损耗而定。相对损耗多的元素其含量将降低,称为“烧损”;相对损耗少的元素,含量将增加,可称“烧增”;为能正确控制熔体的化学成分,在选配金属炉料时,应考虑到熔炼后的变化,在各元素加入量上进行相应的补偿。
在实际的熔炼中,合金中元素的烧损程度,还受原材料品质、熔剂及炉渣、操作技术、特别是生成氧化物的性质的影响。
2.4 熔炼过程中气体和氧化物的防止
前面已经谈到,铝液中气体及氧化夹杂的主要来源是H2O,而H2O则是从搅入铝液的表面氧化膜上、炉料表面(特别是受潮气腐蚀的炉料)、熔化浇注工具以及精炼剂、变质剂中带入铝液。而搅入铝液的氧化膜以及夹杂物较多的低品级炉料(如溅渣、碎块重熔锭)将在铝液中形成氧化物夹杂物。为此,应从熔炼浇注过程中注意下列各点:
①坩锅和熔化浇注工具
使用前应仔细地除去粘附在表面的铁锈、氧化渣、旧涂料层等脏物,然后涂上新涂料,预热烘干后方可使用。熔化浇注工具和转运铝液的坩锅在使用前均应充分预热。
②炉料
炉料在使用前应保存在干燥处,如炉料已经受潮气腐蚀则在配料前进行吹砂以除去表面腐蚀层。回炉料表面常常粘附砂子(SiO2),部分SiO2和铝液会发生下列反应:
4Al+3SiO2 → 2Al2O3 + 3Si
所生成的Al2O3及剩余SiO2均在铝液中形成氧化夹杂,故在加这类料前也应经吹砂后使用。由切屑、溅渣等重熔铸成锭的三级回炉料中常含有较多氧化夹杂物及气体,故其使用量应受到严格的限制,一般不超过炉料总量的15%,对重要铸件则应完全不用。炉料表面也不应有油污、切削冷却液等物,因为各种油脂都是具有复杂结构的碳氢化合物,油脂受热而带入氢。
炉料在加入铝液时必须预热至150~180℃以上,预热的目的一方面时是为了安全,防止铝液与凝结在冷炉料表面上的水分相遇而发生爆炸事故;另一方面是为防止将气体和夹杂物带入铝液。
③精炼剂、变质剂
因其中有些组元很易吸收大气中的水分而潮解,有些则本身含有结晶水。因此,在使用前应经充分烘干,某些物质如ZnCl2则需经重熔去水份后方能使用。
④熔化、浇注过程的操作
熔化搅拌铝液应平稳,尽量不使表面氧化膜及空气搅入铝液中。应尽量减少铝液的转注次数,转注时应减低液流的下落高度和减少飞溅。浇注时浇包嘴应尽量接近浇口杯以减少液流的下落高度,并应匀速浇注,使铝液的飞溅及涡流减至最少。在浇注完铸件后,勺中剩下的铝液不应倒回坩埚而浇入锭模,否则将使铝液中氧化夹杂不断增加。在坩埚底部约50~100mm深处的铝液中沉积有较多量的Al2O3等夹杂物,因此不能用来浇注铸件。
⑤熔炼温度、熔炼及浇注过程的持续时间
升高温度将加速铝液与H2O、O2之间反应,氢在铝液的溶解度也随熔炼温度的升高而急剧增加,当温度高于900℃时,铝液表面氧化膜成为不致密的,更使上述反应显著加剧,故大多数铝合金的熔炼温度一般不超过760℃。至于铝液表面氧化保护膜疏松的铝-镁合金,铝液与H2O、O2间的反应对温度的升高更为敏感,因此对铝镁合金的熔炼温度限制更严(一般不超过700℃)。
熔炼及浇注过程的持续时间(尤其是精炼后至浇注完毕相距的时间)越长,则铝液中之气体及氧化夹杂物含量也越高。因此,应尽量缩短熔炼及浇注的持续时间,特别是应尽量缩短精炼至浇注完毕的时间,工厂中一般要求规定在精炼后2小时内浇完,如浇不完则应重新精炼,在天气潮湿地区以及铸件要求针孔度级别较高,或是易产生气孔、夹杂的合金,则浇注时间应限制得更短。
2.4 再生铝的精炼
当金属熔化成分调整完毕后,接下来就是铝液的精炼工序。铝合金精炼的目的是经过采取除气、除杂措施后获得高清洁度的、低含气量的合金液。精炼有下列几种方法:
加入氯化物(ZnCl2、MnCl2、AlCl3、C2Cl6、TiCl4等);
通气法(通入N2、、Cl2 或N2 和Cl2 混合物);
真空处理法;
添加无毒精炼剂法;
超声波处理
按其原理来说,精炼工序有二方面的功能:对溶解态的氢,主要依靠扩散作用使氢脱离铝液;对氧化物夹杂,主要通过加入熔剂或气泡等介质表面的吸附作用来去除。
三、除气
一般都是采用浮游法来除气,其原理是在铝液中通入某种不含氢的气体产生气泡,利用这些气泡在上浮过程中将溶解的氢带出铝液,逸入大气。为了得到较好的精炼效果,应使导入气体的铁管尽量压入熔池深处,铁管下端距离坩锅底部100~150毫米,以使气泡上浮的行程加长,同时又不至于把沉于铝液底部的夹杂物搅起。通入气体时应使铁管在铝液内缓慢地横向移动,以使熔池各处均有气泡通过。尽量采用较低地通气压力和速度,因为这样形成的气泡较小,扩大了气泡的表面积,且由于气泡小,上浮速度也慢,因而能去除较多的夹杂和气体。同时,为保证良好的精炼效果,精炼温度的选择应适当,温度过高则生成的气泡较大而很快上浮,使精炼效果变差。温度过低时铝液的粘度较大,不利于铝液中的气体充分排出,同样也会降低精炼效果。
用超声波处理铝液也能有效地除气。它的原理是通过向铝液中通入弹性波,在铝液内引起“空穴”现象,这样就破坏了铝液结构的连续性,产生了无数显微真空穴,溶于铝液中的氢就迅速地逸入这些空穴中成为气泡核心,继续长大后呈气泡状逸出铝液,从而达到精炼效果。
3.1 除杂
对于非金属夹杂,使用气体精炼方法能够有效去除,对于要求较高的材料还可以在浇注过程中采用过滤网的方法或使熔体通过熔融熔剂层进行机械过滤等来去除。
对于金属杂质,一般的处理方法是化有害因素为有利因素。即通过合金化方法将其变为有益的第二相,以利于材料性能的发挥。如果一定要去除的,多数情况下是利用不同元素沸点差异进行高温低压选择性蒸馏,来达到除去金属杂质的目的。
由含铝废料熔炼成的铝合金往往含有超标的金属元素,应尽量将其除去。可以采用选择性氧化,可将与氧亲和力比铝与氧亲和力大的各种金属杂质从熔体中除去。例如,镁、锌、钙、锆等元素,通过搅拌熔体而加快这些杂质元素的氧化,这些金属氧化物不溶于铝液中而进入渣中,这样就可以通过撇渣而将其从铝熔体中去除。
还可以利用溶解度的差异的方法来除去合金中的金属杂质。例如将被杂质污染的铝合金与能很好溶解铝而不溶解杂质的金属共熔,然后用过滤的方法分离出铝合金液体,然后用真空蒸馏法将加入的金属除去。通常用加入镁、锌、汞来除去铝中的铁、硅和其他杂质,然后用真空蒸馏法脱除这些加入的金属。例如将被杂质污染的铝合金与30%的镁共熔后,在近于共晶温度下将合金静置一段时间,滤去含铁和硅的初析出晶相,再在850℃下真空脱镁,此时蒸气压高的杂质如锌、铅等也与镁一起脱除,除镁后的纯净铝合金即可铸锭。
为了进一步提高铝合金液质量,或者某些牌号铝合金要求严格控制含氢量及夹杂物时,可采用联合精炼法,即同时使用两种精炼方法。比如氯盐-过滤联合精炼,吹氩-熔剂联合精炼等方法都能获得比单一精炼更好的效果。
3.2 组织控制与变质处理
3.2.1 亚共晶和共晶型铝硅合金的变质处理
铝硅合金共晶体中的硅相在自发生长条件下会长成片状,甚至出现粗大的多角形板状硅相,这些形态的硅相将严重的割裂Al基体,在Si相的尖端和棱角处引起应力集中,合金容易沿晶粒的边界处,或者板状Si本身开裂而形成裂纹,使合金变脆,机械性能特别是延伸率显著降低,切削加工功能也不好。为了改变硅的存在状态,提高合金的力学性能,长期以来一直采用变质处理技术。
对共晶硅有变质效果的元素有:钠(Na),锶(Sr),硫(S),镧(La),铈(Ce),锑(Sb),碲(Te)等。目前研究主要集中在钠,锶,稀土等几种变质剂上。
一:钠变质(Na)
钠是最早而最有效的共晶硅变质元素,加入方式有金属钠,钠盐及碳酸钠三种。
金属钠 最初采用的变质剂是金属Na,钠的变质效果最佳,可以有效的细化共晶组织,加入较小的量(约0.005%~0.01%),即可把共晶硅相从针状变质成为完全均匀的纤维状。但采用金属Na变质存在一些缺点,首先变质温度为740℃,已接近Na的沸点(892℃),因此铝液容易沸腾,产生飞溅,促使铝液氧化吸气,操作不安全,其次,Na比重小(0.97),变质时富集在铝液表面层,使上层铝液变质过度,底部则变质不足,变质效果极不稳定. 同时,Na极易与水气反应生成氢气,增加铝液的含气量。Na化学性质非常活泼,在空气中极易和氧气等反应,一般要浸泡在煤油中保存,在使用前必须除去煤油,这也是一件难度很大的事情,但不除去又会给铝液中带入气体和夹杂。
钠盐 生产中一般应用的变质剂是含NaF等卤盐的混合物,利用钠盐和铝反应生成钠而起变质作用。但这些钠盐极易带入水气,会增大合金吸气氧化倾向,同时这些钠盐对环境具有腐蚀作用,对身体健康有损害。
碳酸钠 以碳酸钠为主的变质剂是应克服采用上述钠盐变质的环保问题而开发的无公害变质剂。也即利用碳酸钠和铝、镁在高温下反应,生成钠而起到变质作用,此反应过程和反应产物都是无毒的。同样,这类无公害变质剂也存在着吸水而增加铝合金吸气氧化倾向的问题。
采用钠变质的还有一个不容忽视的缺点就是变质效果维持时间短,即是一种非长效变质剂。Na盐变质剂的有效期只有30~60min,超过此时间,变质效果自行消失,温度愈高,失效也愈快,因此,要求变质过的铝液必须在短时间内用掉,重熔时,必须重新变质。而且,精确控制钠变质过程是困难的。所以,目前在不少场合,钠变质正逐渐被一些长效变质方法所取代。
二:锶变质(Sr)
锶(Sr)是一种长效变质剂,变质效果与Na相当,且不存在Na变质的缺点,是颇有前途的变质剂。英国、荷兰等国从80年代初就开始推广应用锶(Sr)变质方法。目前,对于锶变质,国内外做了不少研究,我国使用锶(Sr)代替Na或Na盐的规模也在日益扩大。Sr变质有如下优点:①变质效果良好,有效期长;②变质操作时,无烟,无毒,不污染环境,不腐蚀设备、工具,不损害健康,操作方便;③易获得满意的力学性能;④回炉料有一定的重熔变质效果;⑤铸件成品率高,综合经济效益显著。但是,实践表明,变质后的合金易产生缩松,并会增加铸件的针孔度,降低合金的致密性,出现力学性能衰退的现象。
三:锑变质(Sb)
锑(Sb)可使共晶硅由针状变为层片状。为获得层片状,其最佳加入范围通常为0.15%~0.2%。它的变质效果不如Na和Sr。加锑变质一个突出优点是变质时间长(8小时以上)。锑的熔点630.5℃,密度为6.68g/Cm3,所以,比较容易控制锑含量,不易造成变质不足和过变质现象,也不增大铝液的吸气与氧化夹杂倾向,但它的变质效果受冷却速度的影响较大,对金属型和冷却较快的铸件有较好的变质效果,但对缓冷的厚壁砂型铸件变质效果不明显,所以使用上受到一定限制。
四:碲变质(Te)
碲是国内研究成的变质剂,碲变质的作用和锑变质相似,其作用是促使硅以片状分枝方式被细化,而不能变为纤维状,但变质效果比锑强。其变质效果具有长效性,变质后经8小时或重熔效果不变。同样的,它的变质效果受冷却速度的影响也较大。
五:钡变质
Ba对共晶Si具有良好的变质作用。与Na,Sr,Sb相比较,Ba的变质效果比较长效,加入量范围宽,加入0.017%到0.2%的Ba,都能获得良好的变质组织。加入Ba后,合金的抗拉强度明显提高,连续重熔,变质效果仍能保持,其变质效果令人满意。采用Ba变质的不足之处是对铸件的壁厚敏感性大,对厚壁铸件的变质效果差,为了获得良好的变质效果,必须快冷。同时,Ba对氯化物敏感,一般不用氯气或氯盐来精炼。
六:稀土变质
稀土在铝及铝合金中应用较早的国家是德国,德国早在第一次世界大战期间就成功的使用了含稀土的铝合金。稀土元素可以达到与钠、锶相似的变质效果,即可使共晶硅由片状变成短棒状和球状,改善合金的性能。而且稀土的变质作用具有相对长效性和重熔稳定性,其变质效果可维持5~7小时,张启运等人对La变质寿命进行检验,含La0.056%的变质合金,经反复熔化-凝固10次仍有变质效果。
稀土由于其化学性质的活泼性,极易与O2 、N2、H2等发生反应,从而起到脱氢、脱氧、去氧化皮等作用,因而可以净化铝液。
总之,稀土在Al-Si合金中兼有精炼和变质的双重效果,变质效果具有相当长效性和重熔稳定性.稀土元素的加入提高了合金的流动性,改善了合金的铸造性能,优化了合金的内在质量。还有一个最大的优点就是加入稀土不产生烟气,对环境不造成污染,顺应了时代发展的需要。
3.3 变质剂的选择
目前铝合金铸造生产中应用最广的是钠盐变质剂,由钠和钾的卤素盐类组成。这类变质剂使用可靠,效果稳定。变质剂的组成中,NaF能起变质作用。与铝液接触后发生如下反应:
3NaF+Al→AlF3+3Na
反应生成的钠进入铝液中,即起变质作用。由于NaF熔点高(992℃),为了降低变质温度,以减少高温下铝液的吸气和氧化,在变质剂中加入NaCl、KCl。加入一定量的NaCl、KCl组成的三元变质剂,其熔点在800℃以下,在一般变质温度下,处于熔融状态,有利于变质的进行,提高变质速度和效果。此外,呈熔融状态的变质剂容易在液面形成一层连续的覆盖层,提高了变质剂的覆盖作用。为此, NaCl、KCl又称为助熔剂。
有的变质剂中加入一定量的冰晶石(Na3AlF6), 这种变质剂具有变质、精炼、覆盖作用,一般称为“通用变质剂”。浇注重要铸件或对铝液的冶金质量要求较高时常采用此变质剂。
在生产中,变质工序一般多在精炼之后、浇注之前进行。变质温度应稍高于浇注温度,而变质剂的熔点最好介于变质温度和浇注温度之间,这样使变质剂在变质时处于液态,并且变质后即可进行浇注,免得停放时间长,造成变质失效。此外,在变质处理完毕后,变质后的熔渣已经变为很稠的固体,便于扒去,不致把残留的熔剂浇入铸型中,形成熔剂夹渣。
选择变质剂时,一般根据所要求的浇注温度来确定变质剂的熔点和变质温度,接着就可以按照所选的变质剂熔点选择合适的变质剂成分。
3.3 变质工艺因素的影响
变质工艺因素主要为:变质温度、变质时间、变质剂种类及用量。
变质温度
温度高些,对变质反应进行有利,钠的回收率高,变质速度快,效果好,但变质温度不能过高,否则会急剧增加的铝液的氧化和吸气,并使铝液中铁杂质增加,降低坩埚的使用寿命。一般来说,变质温度应选择在稍高于浇注温度为宜。这样避免了变质温度过高,可以减少变质后调整温度的时间,有利于提高变质效果和铝液的冶金质量。
变质时间
变质温度越高以及铝液和变质剂接触的状况越好,则所需的变质时间就越短。变质时间应按具体情况,在实验的基础上确定。变质时间太短,则变质反应进行不完全;变质时间过长,会增加变质剂的烧损,增加合金的吸气和氧化。
变质时间由两部分组成:变质剂覆盖时间一般为10~15分钟,压入时间一般为2~3分钟。
变质剂种类及用量
应根据合金的种类、铸造工艺及对组织控制的具体要求,来选择合适的变质剂种类及用量。选择无毒、无污染并有长效变质效果的变质剂是目前铝合金熔炼工艺的发展方向。
在生产实践中,应考虑到变质剂反应可能进行不完全,所以变质剂用量不能过少,否则变质效果不好。但变质剂用量也不宜过多,否则会产生过变质现象。因此,变质剂用量一般规定为占炉料重量的1~3%。在生产中,通常加入2%就可以保证良好的变质效果。对于金属型铸造的铸件,变质剂用量可适当减少。当采用通用变质剂时,除了考虑变质效果外,还要考虑对这种变质剂的覆盖、精炼能力的要求,通常其变质剂用量为铝液重量的2~3%。
3.4 变质处理的炉前检验
浇注试样,冷却后敲开,根据断口形状判断变质效果。
若变质不足,则晶粒粗大,断口呈灰暗色,并有发亮光的硅晶粒可见。
若变质正常,则晶粒较细,断口呈白色丝绒状,没有硅晶粒亮点。
若变质过度,则晶粒也粗大,断口呈现蓝灰色,有硅的亮晶点。
3.5 过共晶铝硅合金变质处理
过共晶Al-Si合金由于含硅量多,使合金的热膨胀系数降低,耐磨性提高,适用于内燃机活塞等耐磨零件。过共晶Al-Si合金组织中存在板状初晶硅和针状共晶硅。初晶硅作为硬质点可提高合金得耐磨性,但因为它硬而脆,对合金机械性能不利,并使合金的切削加工性能变坏,因此,过共晶Al-Si合金中的共晶硅和初晶硅都要进行变质处理。
长期以来,初晶硅的细化得到了深入的研究。采用超声波振动结晶法,急冷法,过热熔化,低温铸造等都能取得一定效果。但是效果最稳定,在工业上最有使用价值的还是加入变质剂。
目前,实际用于生产的变质剂是磷单质。赤磷使用最早,当加入量为合金重量的0.5%时,即可使初晶硅细化。但由于磷的燃点低(240℃),运送不安全,变质时,磷会激烈燃烧,产生大量烟雾,污染空气,同时也使铝液吸收更多的气体,所以磷多与其他化合物混合使用。现在工业上比较常用的方法是以Cu-P中间合金形式加入。中间合金含磷量一般为8%~10%。加入量在0.5%~0.8%之间。
关于磷对铝硅合金变质的机理,一般认为是磷在合金液中与Al形成大量高熔点的AlP质点,AlP与硅相的晶体结构相似,晶格常数相近,AlP属闪锌矿型结构,晶格常数a=5.451,熔点为1060℃,Si晶体的晶格常数a=5.428,AlP与硅的最小原子间距离也十分相近,硅为2.44,AlP为2.56,AlP可作为初生硅的非自发核心,从而细化初生硅。
来源:铝材那些事
广州致远新材料科技有限公司是一家以生产铝合金锭和锌合金锭为主,集科研、生产、营销为一体的有色金属合金制造企业,获得“国家高新技术企业”的认定,拥有自己的金属材料研究所,,并被认定为“广州市企业研发机构”、“广东省铝合金新材料工程技术研究中心”、“省专精特新中小企业”、“省知识产权示范企业”。可按国家标准以及美国、日本、欧盟等国家和地区的标准生产铝合金材料和锌合金材料,并能按照客户特定要求,研发生产特殊性能的铝合金和锌合金材料。欢迎广大客商洽谈合作,共同发展!
地址:广东省广州市南沙区大岗镇新沙村沙东街268号;
热线:+86-020-84999669、+86-020-84995959、+86-020-34931118;
传真:+86-020-84995353;
电邮:zyalloy@zyalloy.com