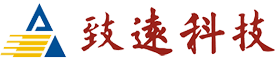
-
- English
一、高熔点和难熔金属的添加和熔化
使用中间合金是合金生产中添加高熔点和难熔金属的有效方法,但在中间合金的制备以及一些特定的环境条件下,不可避免地要进行高熔点金属的直接熔化的操作。
金属硅块、电解铜板在液态原铝(或合金熔体)中的添加和熔化的操作步骤及要领如下:(其他的高熔点和难熔金属的熔化,可调整对应的参数,参考以下步骤操作)
1.设定产量(一般以熔炼炉容量的80%设定),计算熔体及加入金属的入炉数量(因金属硅易烧损,计算时考虑98%的实收率);
2.待加入金属细化:
⑴ 金属硅块的人工破碎:用手锤将大块破至30-40mm粒径,不能过细,尽量使颗粒均匀;
⑵ 电解铜板的机械切割:用剪板机将阴极铜板剪成80×160mm左右的小块。
3.颗粒(或块)的计量入炉(入炉数量应比计算入炉量稍低,须将金属块均匀
地铺于熔炼炉底);
4.液态原铝(或合金熔体)入炉(入炉应迅速,必须使熔体完全浸没所有金属块),记录准确的入炉数量;
5.根据熔体入炉数量,计算补充金属块并入炉;
6.调整炉温(熔硅时调整熔体温度到950℃;熔铜800℃)并保温(调整和保温共35分钟);
7.搅拌熔体(搅拌应迅速、彻底,须避免搅拌后金属块集中成堆);
8.重复一遍调温保温、搅拌过程(要领相同);
9.取样分析熔体中所熔金属含量,若熔化已完成,可进行下一步操作,否则要重复调温保温、搅拌过程直到所加金属完全熔化;
10.最终搅拌,调整熔体温度(熔硅调整到780℃、熔铜720℃)后,开始浇铸。
三、相关知识
中间合金:
㈠ 中间合金的特性
纯金属的熔点一般都较含有一定量其他金属的合金为高。对于确定的两种金属(设如金属X和金属Y),存在着它们确定的熔点(Tx、Ty),当向金属X中逐步加入金属Y时,其熔点由Tx逐步降低;当金属Y的含量达到某一数值时,熔点达到最低点,进一步增加金属Y的含量,熔点开始上升,这时可看作在合金中减少了金属X的含量。如下图就是金属X和金属Y所组成合金的熔点与金属含量的关系图。图1-1中的横坐标表示金属的相对含量,从左至右金属Y的含量逐渐增加,金属X的含量逐渐减少,在每一点两种金属含量之和都是100%;纵坐标为温度轴;图中实线所示为对应金属含量的合金熔点。
图中可见,在图中水平虚线所示的温度T0下时,合金中金属Y的含量必须在大于a而小于b的范围时,其熔点才能低于温度T0。对于两种确定的金属,一般状态下它们的关系图也是确定的。
中间合金就是根据上述原理,使用原铝与高熔点金属预先制备的合金,通过调整高熔点金属的含量,可以使中间合金的熔点满足正常合金熔炼温度的要求,并使中间合金中高熔点金属的含量尽可能高,以便于合金生产的配料。
㈡ 使用中间合金的意义
一些金属元素自身的熔点很高(如镍的熔点为1452℃),若在合金生产中加入纯金属,就必须将铝过热很高的温度,这样不仅会增加铝的烧损,而且恶化了合金的质量。所以,在合金生产中,常将高熔点难熔金属先制备成含量较高的铝基中间合金,这些中间合金的熔点大大低于纯金属,如将金属硅制备成含硅10%左右的中间合金(即102合金),这样以中间合金的形式加入,可以在较低的温度下进行熔炼,目的就是防止金属过热,缩短熔炼时间,降低金属烧损,便于加入高熔点、难熔及易氧化挥发的合金元素,易获得成分均匀、准确的合金。
四、注意事项
1.在金属硅块入炉前,应先将待入炉的熔体准备妥当,以便硅块入炉后能立即将熔体放入炉内淹没硅块,避免硅块表面氧化后难于熔化;
2.为避免金属过烧,熔炼温度最高不能超过:熔硅时1050℃、熔铜时850℃
二、熔体含氢量的测量
使用测氢仪测量熔体氢含量的步骤及操作要领如下:
1.肉眼观察检查测氢仪集气探头、测温探头是否完好,如有损坏应立即更换;
2.检查各联接管路及接头是否完好牢靠、氮气压力是否符合使用要求并做相应的调整;
3.将测氢仪(探头部分)移至熔体待测点位置;
4.将双探头移到熔体上10mm左右预热,同时将测氢仪的电源接头连接妥当;
5.开启测氢仪电源开关;
6.按下氮气吹扫按钮,在十秒钟内将探头移到熔体平面下10-15mm之间,并按下测氢开始按钮(对静止的熔体进行测氢时,须开启探头摇动装置)开始测氢;
7.结束时测氢仪自动进行吹扫,在吹扫过程中将探头移出熔体,完成一个测量过程。此时可重复上一条进行另一次测氢,也可取出测量记录、关闭测氢仪电源结束测氢。
三、相关知识
测氢仪的结构及工作原理:
一般测氢仪由主机部分和探头两部分组成。探头包括测氢集气探头和热电偶测温探头,测氢集气探头通过两根空心金属软管与主机相连;热电偶探头则通过普通的电信号线与主机连接。两种探头由夹具固定在一个水平摇摆装置上,其相对位置可预先调节,通常热电偶探头顶端位置较集气探头更靠下(防止测氢过程中集气探头接触底部造成损坏)。主机部分包括一个氮气瓶、含氢氮气分析装置、吹扫和循环氮气的驱动装置及显示、打印、机架等设施。
测氢时由瓶中导出一定数量的氮气,在被测熔体与含氢氮气分析装置之间形成一个封闭的循环系统。其中的氮气由一根空心管压入熔体,与熔体短暂接触后由另一空心管抽回到含氢氮气分析装置,经含氢氮气分析装置进行快速分析后再次由前一根管压入熔体,如此不断循环。当氮气气泡与熔体接触时,熔体所含氢经气-液界面扩散进入氮气气泡,并被抽出进行分析。随着循环的进行,氮气含氢浓度不断提高,达到一定数值后时,含氢氮气分析装置给出的氢分压数值趋于稳定,表示界面扩散达到平衡,氮气含氢浓度不再提高,此时得到的氮气氢分压数值,结合当时所测出的熔体温度,即可换算出熔体中的氢含量。
测氢仪的测氢工作原理如图1-2所示:
为避免熔体进入管路发生堵塞,测氢开始和结束时都要用氮气对管路进行吹扫。吹扫时两根空心管都做出气管,一般吹扫三次,总共10-15秒钟。
四、注意事项
1.由于集气探头很容易损坏,将探头放入熔体时应特别仔细并进行预热;
2.因集气管很细,很少的熔体进入就能造成管路堵塞,因此在测氢的前、后都必须进行吹扫。
三、产品内部质量缺陷
㈠ 合金锭
在水平铸造生产中,如果生产铝母线,属含有一定杂质的工业纯铝,偏析产生较少,会产生裂纹、气孔和缩孔,生产铝合金锭时,不但产生偏析、气孔、缩孔夹渣等,而且裂纹是造成铸锭废品的主要因素,裂纹有时整根铸锭都有,有时局部都有,从外观观察,有的裂纹在表面很明显,有的裂纹从外面根本看不出来,只有锯切后或通过采取一定手段检测方能发现。
1.中心裂纹的防止
⑴ 应严格控制铸造速度,铸造温度
⑵ 严格按产品质量标准和工艺要求控制合金的化学成分和杂质含量。
⑶ 严格控制炉内温度和浇铸温度。
2.气孔的防止
⑴ 应使铝熔体在炉内停留的时间缩短。
⑵ 采取有效的除气精炼方法。
⑶ 适当提高铸造温度,降低铸造速度。
3.缩孔和疏松防止
⑴ 适当提高浇铸温度,降低浇铸速度。
⑵ 防止熔体在炉中停留时间过长。
4.夹渣的防止
⑴ 应严格按要求采取适当的方式除去非金属夹杂物。
⑵ 适当提高铸造温度,使渣较易上浮除去。
⑶ 操作中尽可能保持中间仓(水平铸造)和结晶器(垂直铸造)的铝液面平稳,不要发生较大波动
㈡ 电工圆铝杆
在铸造生产过程中,不同的产品存在着不同的内部质量缺陷。对于重熔用铝锭,其主要的质量缺陷是外部缺陷,如:飞边,大、小块,表面积渣等,而对它的内部缺陷要求不高,但必须保证其内部化学成份均匀。而对于电工圆铝杆其内部的质量缺陷主要有气孔和夹渣。
1.气孔
气孔对电工圆铝杆的性能有着很大的影响,当浇铸时,铸坯内部气孔含量过多,可能导致在轧制过程中出现断线或在缠卷过程中被拉断,气孔产生的影响因素主要有:
⑴ 铝液温度过高,导致含氢量过高。根据试验表面,铝液内部的含氢量与铝液温度成正比。
⑵ 在浇铸过程中,冷却水冷却产生的大量蒸汽没有及时散去,部分蒸汽被溶入到铝液内部形成气孔。
⑶ 钢带上润滑油太少,没有形成较好的一层保护油膜,造成蒸汽进入铝液。
主要措施:
⑴ 降低铝液温度,保证铝液温度在正常的浇铸温度范围内。
⑵ 在浇铸前安装除气装置,如用高纯氮气或氮—氯混合气体等除气或在保持炉内进行除气处理。
⑶ 在浇铸部位安装风扇将蒸汽吹散。
⑷ 在浇铸过程中,调整好润滑油量,保证钢带上有一层保护油膜。
2.内部夹渣
夹渣同样对电工圆铝杆的性能有很大影响,在生产过程中,可能导致断坯或断线。夹渣产生的影响因素主要有:
⑴ 铝液内部含渣过多,没有进行有效的精炼处理。
⑵ 铝液温度过高,产生较多的氧化浮渣。
⑶ 铝液在流槽转注过程中,没有使用TD管和浮漂,使铝液不断冲刷,造成渣子溶入铝液中。
主要措施:
⑴ 在保持炉内对铝液进行精炼,如加入精炼剂、造渣剂等,保证铝液静置时间。
⑵ 做好保持炉温度控制,确保铝液温度在标准范围内。
⑶ 在浇铸前加入过滤装置,如使用陶瓷过滤板进行过滤。
⑷ 在流槽转注过程使用TD管和浮漂,使铝液在氧化膜下层流动,保持液面平稳,避免将氧化渣冲入铝液中。
不管是气孔还是夹渣,都可以降低电工圆铝杆的抗拉强度和延伸率以及增加它的电阻率,并且影响电工圆铝杆的正常生产。
三、相关知识
一般重熔用铝锭质量的要求有两方面:一是化学成分要符合国家标准,二是铝锭表面无夹渣、飞边,较大的波纹、缩孔等。
对于变形铝合金及可加工使用的铸造铝合金,除要求化学成份、表面冷隔、拉裂的深度、疱瘤(偏析瘤、软熔瘤和金属瘤)的高度,表面夹渣的面积和深度,还
要求铸锭和铸坯的几何尺寸符合加工要求,铸锭组织细小、致密、均匀,符合有关技术标准。铸锭组织细小指晶粒小、晶内结构细;致密指破坏铸锭连续性的缺陷如疏松、气孔、夹渣、裂纹等程度小,均匀指柱状晶、羽毛晶、粗大等晶等缺陷造成组织不均一的程度,并且铸锭内化学成分应分布均匀,各种偏析的程度。由此可见,造成铸锭内部质量缺陷的原因很多,但常见的主要是裂纹、气孔、疏松、缩孔、偏析、夹渣等。
在生产过程中,铸锭的内部质量状况是无法观察到的,只有在锯切后可观察到锯切部位的裂纹、缩孔,而铸锭的内部质量状况直接影响到铸锭的使用性能和加工性能。而其它需通过低倍试片检验,断口检验,超声波无损检验、机械性能检验等才能发现和确定。了解铸锭内部质量缺陷产生的原因及影响因素,对于在生产中采取有效措施提高及改善铸锭质量有着重要意义。
在了解裂纹、气孔、疏松、缩孔、偏析、夹渣产生的原因之前,先了解一下收缩、铸造应力和液穴的概念。
1.收缩
金属在液态、凝固态和固态的冷却过程中,体积都要发生变化,对于铝合金而言从铸造温度到常温,不管中途体积如何变化,最后体积是缩小,这一现象称为收缩,热脆性就是指合金在高温状态下形成热裂纹的倾向性。
2.铸造应力
铸造应力产生的基本原因是:铸锭在结晶和冷却过程中,由于径向和轴向的收缩受到阻碍而形成,按其形成的机理一般可分为三种:机械应力是因铸模、结晶器等对金属收缩的阻碍和对金属的相对运动产生磨擦作用而产生的;相变应力是金属相变(由液态变为固态)时伴随体积的变化并相互阻碍而产生的;热应力是铸锭在冷凝过程中由于温度差产生的,减小这些应力的基本措施是:增加结晶器内表面的光洁度,均匀润滑,均匀供流,均匀冷却,降低浇铸温度和速度,减小二次冷却程度等。
3.液穴
液穴是被结晶前沿(液态金属与凝固层的边界)所包围的液体金属区域,结晶面的形状即是液穴形状,液穴的深度直接反映了铸锭的凝固时间和凝固速度。而液穴的形状又决定着沿铸锭断面结晶速度变化的性质。因此,液穴深度和形状是控制铸锭结晶组织的重要指标,测定和调整铸造过程中液穴的深度是控制铸锭质量的重要手段。
在垂直铸造时,通常液穴的形状较浅,水平铸造时液穴的形状较深,这是因为水平铸造的铸造速度比垂直铸造快,冷却能力小而导致的。
影响铸锭液穴深度的因素有:
⑴ 合金的物理性质,对于各种变形铝合金、液穴的深度主要与合金的导热性有关。
⑵ 铸锭的形状和尺寸,其它条件相同时,液穴深度与铸锭厚度、直径壁厚的平方成正比;当圆铸锭直径等于扁铸锭厚度时,扁铸锭液穴深度比圆铸锭大一些,空心铸锭的液穴深度小于同外径实心圆铸锭的液穴深度,且内径越小,深度越接近。
⑶ 铸造工艺参数,在其它条件相同时,液穴深度随冷却强度的降低,铸造速度的提高,铸造温度的提高,结晶器有效高度的增加而加深。
液穴的深度可以用探棒(垂直铸造常采用)和倾出法(水平铸造常采用)进行实测,也可加入能改变铸锭组织的添加物或放射性元素来指示的方法测定;用在铸锭内凝入热电偶来研究温度场的方法测定。
㈠ 裂纹
裂纹是铝合金铸锭生产中最普遍的一种缺陷。在生产大规格圆锭,空心锭和扁锭时,裂纹更是个突出的问题,通常铸锭中的裂纹分为两种:在凝固过程中产生的裂纹称为热裂纹;在凝固后的冷却过程中产生的裂纹称为冷裂纹。两种裂纹的特征不同:热裂纹多沿着晶界曲折而不规则,常出现分枝,表面略呈氧化色(灰黑色)裂纹时没有响声,也叫结晶裂纹,而冷裂纹往往贯穿晶粒内部,裂纹平直而较规则,表面呈洁亮的银白色,裂纹时往往伴随有清脆的响声。在实际生产中,也经常出现先是热裂纹,而后由于应力集中形成冷裂纹的混合型裂纹,铸锭中的热裂纹和冷裂纹严重地破坏了制品组织的连续性。
1.裂纹产生的原因
裂纹是在金属的强度与塑性无法承受铸造应力作用就产生开裂。
影响热裂纹的因素很多,主要是:
⑴ 化学成分的影响,对于不同牌号的合金,或是对于同一合金,在允许范围内主要组元的含量不同,以及合金中杂质的含量和比例不同,铸锭结晶时的体(线)收缩量不同。
⑵ 结晶组织的影响,晶粒的细化,可以降低线收缩开始速度,并减小线收缩缝,而降低合金的热裂倾向性。
⑶ 铸造条件和工艺因素的影响,提高熔炼温度和铸造温度,提高冷却速度,铸造速度,局部供水不均和供流不均会增大形成热裂纹的倾向性。
影响冷裂纹的因素主要是:
⑴ 合金在低温时的塑性,随着合金塑性降低,铸锭形成冷裂纹的倾向增大。
⑵ 有害杂质和非金属夹杂物的含量,铝合金中铁、硅的含量和比例增大会降低铸锭塑性,非金属夹杂物破坏铸锭连续性,并引起应力集中增大产生冷裂纹的倾向。
⑶ 铸锭形状和截面尺寸,圆铸锭随直径增大,塑性降低,形成冷裂纹的倾向急剧增大;空心圆锭随外径增大,壁厚减薄,冷裂倾向增 大;扁铸锭随宽厚比增大和在宽厚比一定的情况下随厚度增大,冷裂纹倾向增大。
⑷ 铸造速度,随铸造速度提高,形成冷裂纹的倾向降低。
⑸ 热裂纹和表面冷隔是应力集中的地方将促使冷热纹的形成。
2.裂纹的形式
连续和半连续铸造时产生裂纹的倾向很大,各种铸造方法和不同形状的铸锭产生裂纹的形式是不一样的,不同形式的裂纹产生的原因和防止裂纹产生应采取的措施也不同,对于圆形铸锭主要有中心裂纹、环状裂纹、径向裂纹,空心铸锭主要有内壁放射状裂纹、环状裂纹、横向裂纹,扁锭主要有底部裂纹、浇口裂纹、侧面裂纹、表面裂纹,如下图所示。对于方锭和厚度较厚的扁锭也存在中心裂纹,其中最常见的裂纹形式就是中心裂纹。1-3、1-4、1-5是几种常见的裂纹形式。
3、中心裂纹
中心裂纹可能是冷裂纹,也可能是热裂纹,当铸锭冷却到一定时间,铸锭内外层温差大,铸锭内层冷却速度大于外层冷却速度,内层的收缩受到早已冷却外层的阻碍,在铸锭的中心部位沿直径平面产生应力,这种应力从结晶瞬间到铸锭完全冷却过程中不断增强,在应力作用下,中心部位产生变形,当应力达到一定的位置,超过金属允许的变形值,铸锭中心使被拉开形成中心裂纹,在铸锭开头和结尾时,由于正常的铸造条件遭到破坏,冷却条件极不均匀,由此产生的附加热应力也是导致中心裂纹的重要因素。
中心裂纹的特点主要是:⑴在所有工业变形铝合金铸锭中均可产生是圆铸锭最常见的一种裂纹形式;⑵在软合金铸锭中表现为热裂纹,在硬合金铸锭中通常表现为中心热裂纹,外围冷裂纹的混合型裂纹;⑶裂纹沿铸锭横截面发展,多数在铸锭中心面相当于直径1/3-1/2的范围内,但有时也可以发展成沿整个直径破裂的通心裂纹;⑷裂纹常在铸锭中心部位出现,可从铸锭底部直到浇口部。
防止中心裂纹的方法主要有:⑴提高合金的高温和低温时塑性,以提高抗热裂的冷裂能力,为此,须按工艺要求控制合金的化学成分和杂质含量,防止熔体过热和在炉内停留的时间过长。⑵调整液穴,降低铸锭内外层的温度差。为此可降低铸造速度或者提高结晶器的高度。
㈡ 气孔、
1.气孔产生的原因
气孔是铸锭内一种内表面光滑的孔洞性缺陷,其形状多呈圆形、椭圆形、针条形。气孔是液态金属在冷却和凝固过程中,以气泡形式析出的气体来不及跑出液面而留在铸锭中形成的,气体的来源在基础知识部分已作说明,溶解在金属熔体中的气体主要是氢。随温度的升高,熔体的含气量也上升,即金属在液态下含氢量较高,而在固态下含氢量很低,金属在结晶时,随着气体的溶解度急剧降低,气体可能会通过扩散从金属液面逸出,或者是在金属液内形成气泡上浮逸出,但是由于金属表面有氧化膜的阻碍,且当结晶速度过大时,气体由金属内部扩散至液面析出比较困难,故多以气泡形式析出,形成的气泡或因粘滞作用和结晶速度太快,来不及逸出金属表面而形成集中的气孔;或因被枝晶包围而阻碍逸出,形成弥散干晶界或枝晶间的疏松性气体。
2.气孔产生的影响因素
液态金属的含气量和铸造时的冷却速度是影响气孔产生的决定因素,其中金属的含气量则起着决定性作用。溶解于液态金属中的气体以气泡形式逸出,在一定的冷却条件下,存在着一个临界含气量,超过此临界值便产生气孔,低于此临界值,可不产生气孔,在半连续铸造条件下,临界含气量还与合金的冷却速度及成分有关。一般来说,冷却速度越大,临界含气量也越大,形成气孔的倾向越小,冷却速度越小,临界含量也越小,产生气孔的倾向越大。
3.防止气孔产生的途径
减少或消除气孔的办法主要是降低熔体内的含气量,为此应缩短熔体在炉内的停留时间,采取有效的除气精炼方法;适当提高铸造温度,降低铸造速度,以有利于气体的逸出,提高冷却速度,阻止气体以气泡形式析出。
㈢ 缩孔与疏松
金属在凝固过程中会发生体积收缩,由于体积收缩得不到补充往往在铸锭最后凝固的部分出现孔洞称为缩孔,体积大而集中的孔洞称为集中缩孔,细小而分散的孔洞称为分散性缩孔,也称为疏松。缩孔的形状不规则,表面不光滑,故可以和气孔区别开来,一般说的缩孔主要是指集中缩孔。
集中缩孔主要产生在铸锭的浇口部,因为铸锭的结晶是由表至里进行的,使液态和凝固收缩量集中到最后凝固的部分,形成集中缩孔,在垂直铸造生产的铸锭中,冷却结晶由下部开始,并且基本上是单向结晶,上部液穴能不断地得到液体的补充,不产生集中缩孔。
疏松是一种细小的分散缩孔和气孔,多分布在铸锭的中心和尾部等最后凝固的部分,疏松的形状不规则,表面不光滑故易与较圆滑的气孔相区别。在铸锭中有些疏松常常被析出的气体所填充,孔壁表面变得较平滑,此时的疏松也是气孔,称为气眼疏松,疏松会减小铸锭在加工变形时受力的有效面积,并在疏松处产生应力集中,显著降低铸锭的机械性能。
防止缩孔和疏松的基本途径是制定合理的铸锭工艺,尽可能使疏松转化为铸锭头部的缩孔,然后通过人工补缩来消除,并可适当提高浇铸温度,降低浇铸速度,加强二次冷却,使液穴浅平等。
㈣ 偏析
在一根铸锭的不同部位取样进行化学分析,发现各点的成分都不相同,各点的成分与铝液的原始成分也不一样,铸锭内这种各部分化学成分不均匀的现象以及形成这种不均匀性的过程叫做偏析。
连续铸造的铝合金铸锭内常见的偏析有枝晶偏析,区域偏析和局部偏析,实际生产中由于合金元素在熔炼时溶解不充分或搅拌不充分或烧损,也可以造成化学成分的差别。
枝晶偏析是属于一个晶粒范围内的显微偏析又叫晶内偏析。在实际铸造条件下所得的固溶体中,每一个树枝晶内各部分的化学成分是不均匀。
区域偏析是指易熔组分在铸锭横截面上有规律性的不均匀分布,根据易熔组分在铸锭横截面上富集的部位,区域偏析可分为正偏析、反偏析、中间偏析三种类型,铸锭中心部分富集易熔组分的区域偏析叫正偏析;铸锭周边层富集易熔组分的区域偏析叫反偏析,易熔组分主要富集在铸锭中心和周边层之间的中间区域时的偏析则叫中间偏析;在连续铸造的铝合金铸锭内,区域偏析主要表现为易熔组分的反偏析。
局部偏析是指铸锭内宏观体积上某些地方化学成份的偶然不均匀性。铝合金棒连续铸锭内的局部偏析主要是由于光亮晶粒和金属化合物的偶然堆放造成的。
由于偏析的存在使铸锭的化学成分和结晶组织局部均匀,使铸锭的性能恶化。在实际生产中偏析是不可避免的,但可以采取一定的措施把偏析控制在允许的范围
内,如控制铸造速度、铸造温度、冷却强度等,还可以对铸锭进行长时间的均匀化处理消除晶内偏析。
㈤ 夹渣
铸锭中单独的颗粒较大或细小成群的非金属夹杂物,称为夹渣。在这里夹渣主要指内部夹渣,内部夹渣一般定在所熔检验中发现,夹渣产生的原因和消除方法在基础知识中已作说明。在实际生产中,夹渣常发生在铸锭的端头部分。
此外,铸锭组织中的其它缺陷还有羽毛状晶、光亮晶粒(也叫浮游晶)、粗大金属间化合物、白点、白斑等。
四、注意事项
1.应严格控制铸造条件。因为铸造条件的改变可能会使不同的组织缺陷向相反的方向发展。
2.铝熔体净化(或精炼)后应及时组织生产,防止因熔体在炉内时间过长造成金属烧损和吸收大量炉气。
四、小 结
通过叙述制备中间合金可降低金属的熔点的基本原理,学习高熔点和难熔金属的加入方式;通过叙述测氢仪的结构与工作原理,了解测氢仪的操作方法,以便能够在生产中正确测量熔体中的氢含量,以保证产品质量;通过学习铝及铝合金产品内部质量缺陷产生的原因及影响因素,以便能够在生产过程中采取有效措施防止内部质量缺陷的产生。
来源:公众号:铝材那些事