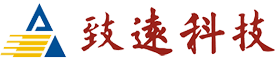
-
- English
微量元素通常是指在铝合金材料中所占比 例小于 1%的过渡族元素,当然,某组元在某合 金中是主要组元,但在另一类合金中则可能成为 微量元素或者杂质。人们通常会忽略微量元素对 材料的影响。正常情况下微量元素也不会在合金 材料中起到破坏作用,但是,当零部件企业所用 铝合金材料来源为再生铝合金铸锭时,微量元素 就是不可忽视的因素了,无论微量程度如何,它 都存在于合金铸锭中,由于它的存在,也必然会 给铸件带来影响。
1 微量元素与再生铝合金铸锭的关系
再生铝合金铸锭的原料基础与铝合金铸锭 的原料基础有着很大的区别,因为前者的原料来 源于废旧回收铝,它的基底原料是已经合金化 后,各种微量元素已经存在其中了,而后者来源 于原铝,它的基底原料为纯铝不含其他合金元 素,因此,当再生铝合金铸锭作为零部件企业的 原料时,在微量元素的限制与添加比例上一成不 变的参照原有铸造铝合金标准显然不适用了。
因为报废的原材料中含有大量的多种金属 和非金属以及杂质,特别是近些年来交通用铝、 通用机械的迅猛发展,终端市场对铸造铝合金零 部件的设计优化和合金强化的多样性,造成了供 给侧的废料变化增快,废料中所含的各种合金元 素的多样性、复杂性和变化性是再生铝合金原料 的一大特点,再生铝合金原料的不可预估性,对 铸件所需材料基底的连续性以及许多无法估计 的缺陷诱发因素都存在着不同程度的影响。当再 生铝合金铸锭作为原料时,不太起眼的所谓微量 元素的影响力不仅存在,而且危害还有可能是巨大的。
我过去接触了很多类似的案例,下游企业常 常因为这些微量元素的原因,造成产品缺陷和不 可预估的损失。很多时候零件铸造加工企业在同 等工艺下批量报废,却苦苦找不到原因,有不了 了之的,也有找再生铝合金铸锭企业扯皮的。要 求赔偿的,退货的等等。查看牌号元素标准,各 种元素都在范围内。但是,恰恰这里有一个不为 人知的一个很大的认知误区—微量元素。
我们现行的铝合金材料标准里元素质量分 数的确定,都是在以原生铝为基底的基础上,通 过计算并且经过大量的试验得出的合金材料的 元素含量与材料性能,换句话说就是基底材质是 比较纯净的,在此基础上得出的相关数据,与合 金化后的废铝作为基底的材质相比,是完全不能 等同的。所以,铸件企业在以后的加工过程中铸 件发生任何变化都有可能了,因此,微量元素的 控制在再生铝合金铸锭中的添加及比例控制就 显得相当重要了。再生铝合金铸锭企业的原料在 不断地发生变化,对原有铸造铝合金标准中微量 元素的限制提出了新的挑战,也显现了材料实际 运用与标准的不适用性。
2 微量元素的利弊
为使基础原料符合下游产品性能要求的,有 必要搞清楚微量元素在再生铝合金原料中的利 与弊。再生铝合金铸锭中常见的微量元素的添加 与比例控制对铸件的品质和性能都有些什么影 响。
(1 )锡(Sn )
锡的熔点为 231 度,锡不仅怕冷,而且怕热。在 161℃以上,白锡又转变成具有斜方晶系的晶 体结构的斜方锡。斜方锡很脆,一敲就碎,延展 性很差,又称作"脆锡"。白锡、灰锡、脆锡,是 锡的三种同素异形体。
锡在合金材料中固溶度极低(<0.01%),锡 和铝不形成化合物,以游离态存在于合金中,沉 淀于铝的等轴晶晶界,结晶范围宽导致非平衡结 晶,由于和铝的熔点差,铸造时往往不能快速冷 却,会造成枝晶间距偏大,铸造中和铝硅共晶体 形成凝固偏析和比重偏析。
过量的锡元素在产品压铸中常出现以下现 象:①脱模困难,产品裂纹,变形。②由于 161℃ 时,该元素晶系偏转,结构产生变化,表现为零 件在取件时显脆性,流道和浇冒口自行脱落,几 乎没有塑性,即使勉强成型后在装机使用中都会 出现热膨胀率大,造成零件特别是箱体零件的冷 裂,密封性不好的缺陷。
鉴于以上原因,根据笔者多年的铝合金铸造 实践经验,建议压铸或者重铸的产品,都应将锡 元素含量控制在 0.01%以下。
(2 )锂(Li )
锂的熔点 180.54℃,密度 0.534 克/厘米³。在 500℃左右容易与铝液里的氢发生反应,生成氢 氧化锂,当铸锭呈液态时,经常表现为,锭表面 好像覆盖了一层厚厚的不透明膜,用挑皮铲刮开 马上又有,始终刮不尽。
产生这种现象的原因是,由于锂的原子半径 很小,比起其他的碱金属,压缩性最小,硬度最 大,熔点最高。当温度处于-117℃前,金属锂是 典型的体心立方结构,熔炼中与铝合金硅铁形成 块状初晶硅和针状铝铁相,颗粒尺寸大而不均 匀,当这些中间相分布在晶界时,形成坚硬的晶 间化合物,另外,熔体净化时与精炼剂中的钾、 钠在室温下以液态共存于晶界并萌生裂纹。
过量锂元素产生的有害物质富集于晶界,降 低了晶粒之间的结合能,降低了合金密度,使得 压铸零件产生冷裂纹,形成气密性和水密性不良 的铸件缺陷,根据笔者多年的反复试验和实践经 验,建议在铝硅系铸造合金中锂元素的含量控制 在 0.001%以下。
(3 )钙(Ca )
钙的熔点 839±2℃。密度 1.54 克/厘米³。属于碱土金属,在元素周期表位于第 4 周期、第 IIA 族。钙在铝中固溶度极低,与铝形成 CaAl 4 化合 物,在变形铝合金中 0.1~0.2%的钙,可以改善 材料的导电性与加工性能。但在铸造铝硅系合金 中,与硅形成硅钙化合物,铸锭表现为颜色发暗 无光泽,铸锭表面有明显的褐色氧化膜堆积团, 很多时候被误认为是渣。当压铸前重熔时,铝液 表面浮现一层黑褐色泡沫状表皮。铸锭凝固过程 中,加快了片状硅的生长速度,热处理可割裂固 溶体强化相。
含钙高的合金锭材料能使铸造零件塑性降 低,特别是低压或砂型铸造铸造后需热处理的零 件,表现为淬火厚薄差过渡带和零件倒角处,开 裂的现象尤为明显,建议在铝硅系合金铸锭中钙 元素的含量限制在 0.003%以下。
(4 )锶(Sr)
锶为碱土金属,表面活性元素,在结晶学上 锶具有改变金属间化合物相的作用。因此,用锶 元素进行变质处理能改善合金的塑性、加工性和 产品质量。
由于锶的变质有效时间长、效果和再现性好 等优点,近年来在 Al-Si 铸造合金中取代了钠的 使用。
在挤压材用铝合金中加入 0.015%~0.03% 锶,使铸棒中 β-AlFeSi 相变成汉字形 α-AlFeSi 相,铸棒均匀化时间减少 60%~70%,提高了材 料力学性能和塑性加工性,改善了制品表面粗糙 度。对于共晶型(10%~13%)的铝合金中加入 0.02%~0.07%(实践中 0.08%)的锶元素作变质 处理,可形成细小的、弥散的 Al 2 Sr、Al 4 Sr 弥散 相,可抑制合金的再结晶和晶粒长大,抑制片状 硅的生长速度,使初晶硅量减少至最低限度,力 学性能也显著提高,材料抗拉强度和屈服强度都 有所提高,延伸率也有所增加。在过共晶 Al-Si 合金中加入锶,能在一定程度上减小初晶硅粒子 尺寸,改善塑性加工性能。近些年来新开发的时 效铝合金,尤其是 Al-Li 系合金中加入该元素, A1 2 Sr 作为 δ 相的形核位置,可以加速时效进程。
(5 )钪(Sc )
钪对铝合金的组织和性能影响是近年来的 热门研究课题。铝合金中加入钪后,会在固溶或 时效过程中析出与基体共格的弥散相 A1 3 Sc,与A1 3 Zr 有相似的作用,但效果更佳。此外 A1 3 Sc 本身细小均匀,可以细化铸态组织,从而改善合 金的焊接性能。
(6 )锆(Zr
锆是铝合金的常用添加剂。一般在铝合金中 加入量为 0.1%~0.3%,锆和铝 形成 Al 3 Zr 化合 物,可阻碍再结晶过程并细化再结晶的晶粒。锆 也能细化铸造组织,但比钛的效果要小。有锆存 在时会降低钛和硼细化晶粒的效果。
在 Al-Zn-Mg-Cu 系合金中,由于锆对淬火敏 感性的影响比铬和锰的小,因此宜用锆来代替铬 和锰细化再结晶组织。在高镁(镁>2%)的铸造 铝硅系合金中加入 0.1~0.2%的锆,铸件的强度 和塑性都会提高。为防止这类合金的钠脆现象, 在精炼剂的选用上最好选用无钠精炼剂。
(7 )稀土(RE )
氯化稀土加入铝合金中,可与 Fe、Si 等形成 高熔点化合物,从而非自发形核使晶粒细化。原 子半径较大的稀土元素对共晶硅有较好的变质 作用,能使夹杂相趋于球化。可减少合金中的气 体和夹杂,还可降低熔体表面张力,增加流动性, 有利于浇注成型。可减小二次枝晶间距,特别是 对于有二次枝晶间距技术要求的汽车零部件,加 入适量的氯化稀土,对工艺性能有着明显的影 响,稀土加入量约为 0.05%~0.1%为宜。
(8 )钠(Na )
钠在铝中几乎不溶解,最大固溶度小于 0.0025%,钠的熔点低(97.8℃),当合金中存在 钠时,在凝固过程中吸附在枝晶表面或晶界,热 加工时,晶界上的钠形成液态吸附层,产生脆性 开裂,形成 NaAlSi 化合物。无游离钠存在时, 则不产生“钠脆”。
合金中当镁含量较高时,镁夺取硅,析出游 离钠,产生“钠脆”。因此高镁铝合金铸锭不允许 使用钠盐熔剂。氯化法可防止“钠脆”,该方法使 钠形成 NaCl 排入渣中。也可加铋使之生成 Na 2 Bi 进入金属基体。加锑生成 Na 3 Sb 或加 入微量的 铍亦可起到相同的作用。
微量的Na可以诱发高纯A1-Mg合金的高温 脆性沿晶断裂,对合金的性能产生十分不利的影 响,前些年由于工业所应用的合金纯度较低,此 问题尚未得到足够的重视。随着材料科学的发展和冶炼技术水平的不断提高,杂质元素含量对合 金性能产生的影响有了新的认识。Al-Mg 合金在 热加工时常常会发生脆性断裂,与 Na 的有害作 用分不开的。比如乘用车方向盘用的铝镁合金 ADT6 和 AIMg 2 Mn,用含钠的精炼剂精炼和无钠 的精炼剂精炼,铸锭在压铸中的流动性和铸件的 成品率就会有很大的差别。
(9 )镉(Cd)
鎘在合金中固熔度极微,吸附于晶界,构成 众多的电极电位差,形成较大的微腐蚀电池,能 使合金晶界结合松弛、粗化(老化),特别是锌 合金,使其晶间腐蚀变得十分敏感,在温、湿环 境中加速了本身的晶间腐蚀,降低了机械性能, 并引起铸件尺寸变化。
当锌合金中杂质元素镉含量过高,工件刚压 铸成型时,表面质量一切正常,但在室温下存放 一段时间(八周至几个月)后,表面出现鼓泡。 铝合金中的镉化合物由于毒性较大,ROHS 指令 中明确为有害物质,其含量限制在100PPM以下。
(10 )铬(Cr )
铬在 Al-Mg-Si 系、Al-Mg-Zn 系、Al-Mg 系 合金中常见的添加元素。当温度达到 600℃时, 铬在铝中的溶解度为 0.8%,室温时基本上不溶 解。过量的铬在铸造铝合金中可形成比重大于熔 体的(FeMnCr) 3 Si 2 Al 15 。 和(CrMn)Al 12 等金属 间化合物,白色呈沙状,密度较大。铸锭重熔过 程中,如遇高温过烧或铝液长时间保温时,常沉 淀于坩埚或炉前熔化炉底部。使接近底部的铝液 对铸造成型产品造成多种缺陷。合金中的 Cr 可 阻碍再结晶的形核和长大过程,对合金有一定的 强化作用,可改善合金韧性,降低应力腐蚀和开 裂敏感性,但会增加淬火敏感性,使阳极氧化膜 呈黄色。
铬在铝合金中的添加量一般不超过 0.35%, 并随合金中过渡元素的增加而降低。六价铬在欧 盟 ROHS 指令中属于有害元素,要求零件中含量 小于 1000PPM 以下。而低压或重铸的零部件, 一般后续都是需要热处理的,所以,合金中铬含 量最好限制在 0.05%以下。
(11 )铅(Pb)
铅是低熔点合金,与 Al 不形成化合物,在 铸造凝固过程中最后凝固,存在于晶界处,材料的抗拉强度和耐蚀性有所降低,当铸锭中含量较 高时,表现为表面氧化加速,特别是在空气湿度 较大的季节尤为明显。但有利于零件的加工切 削。合金作稀土变质,可抑制有害影响,在 ROHS 指令中铅为有害物质,其含量应限制在 1000PPM 以下。
3 结论
以上仅围绕几种易熔相合金元素,简述了微 量元素与再生铝铸造合金锭的关系与利弊,除此 之外,微量元素的影响还与零部件企业的铸造形 式相关,在压力铸造中,材料基底中的微量元素 对铸件的影响相对较小,对母金属的纯度要求不 太高。但在砂型铸造(S)和低压铸造这些补缩 能力较弱或者后续工艺需要进行热处理的,材料 基底中的微量元素对铸件的影响相对较大,因 此,这类零部件加工企业最好采用基底较为纯净 的原料作为母金属或进行稀土变质,形成少量稀 土化合物,以减少微量元素对铸件的危害性从而 提高铸件的性能与产品的成品率。